Experts in the Field are a Part of OBIC’s Commitment to Highly Trained, High-Quality People
Trey Hesselschwardt is the Chief Training Officer with OBIC and has been with the company since its founding. What does a Chief Training Officer do? First, he helps new applicators come on board with equipment training and OBIC’s process methodology. Second, he answers questions via phone calls on a daily basis. Third, he travels around the world to visit installers in-person, walks through situations they’ve never experienced before, and navigates through that with the best OBIC product choices. He makes 2 or 3 visits per month, with the goal to see every applicator at least once per year or more.
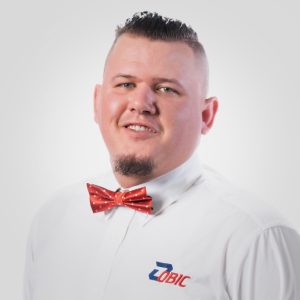
Trey Hesselschwardt
“I want to empower our applicators by teaching and giving them the tools to succeed. The best part of my job is the ability to help people and to watch them do something they couldn’t do or didn’t know before,” he said.
The service that this position delivers is a true differentiator over other companies. “A lot of suppliers will sell you a product and say, ‘good luck.’ Our value is we’re not going to do that. I’ll randomly call an installer and say, “I haven’t heard from you in awhile so what’s going on.” We want everyone to know that OBIC is a leader in protective coatings. You’re going to succeed because we will make you succeed. It’s part of OBIC’s commitment to highly trained, high-quality people,” said Trey.
One example of this service took place last fall, when one of the OBIC-certified installers, Precision Trenchless, was working on a project in Kingston, New York. They asked Trey to come and be on hand to assist as they were lining the largest tank they’d ever done and wanted to ensure that the application and process was correct for a tank that size. In addition, they were going to be conducting holiday spark testing and wanted to confirm proper utilization of that device.
Jason Hickling, Foreman with Precision Trenchless, was managing the City of Kingston project where Precision was installing a new OBIC Armor 1000 Polyurea Lining System for each tank at the wastewater treatment plant.
The tanks involved were open-top, rectangular 350,000-gallon concrete bubbler tanks. The main challenge was that each tank shared a wall with the next one and because they were only able to drain the specific tank they were lining, the tank that was next to it still had water in it, leading to some exfiltration into the tank being lined. Trey was on hand to help with planning and offering guidance on how best to execute a tank this large. He assured product specification quality control utilizing a coating thickness instrument that measured proper application density. Working together, they made sure everything was up to the OBIC standard.
“It was great to see how good the OBIC product worked,” said Jason. “There was no infiltration of the shared wall after it was lined. Trey took the time needed to ensure we were running properly. He is very thorough, and the support is amazing. I know I can call at any time. After Trey’s guidance, it was a game changer for me and a whole different ballpark in terms of how to spray the lining system.”
Interested in becoming an installer like Precision Trenchless? OBIC water and wastewater structure rehabilitation products are in demand throughout the United States and beyond. To accommodate this demand, we are always on the lookout for qualified installers interested in joining the OBIC team. In addition to building an installer network in the U.S., we are also looking to expand our team globally. Learn more about the qualifications of becoming an OBIC installer on our website or give us a call at 866-636-4854 to discuss the advantages of joining the OBIC team.